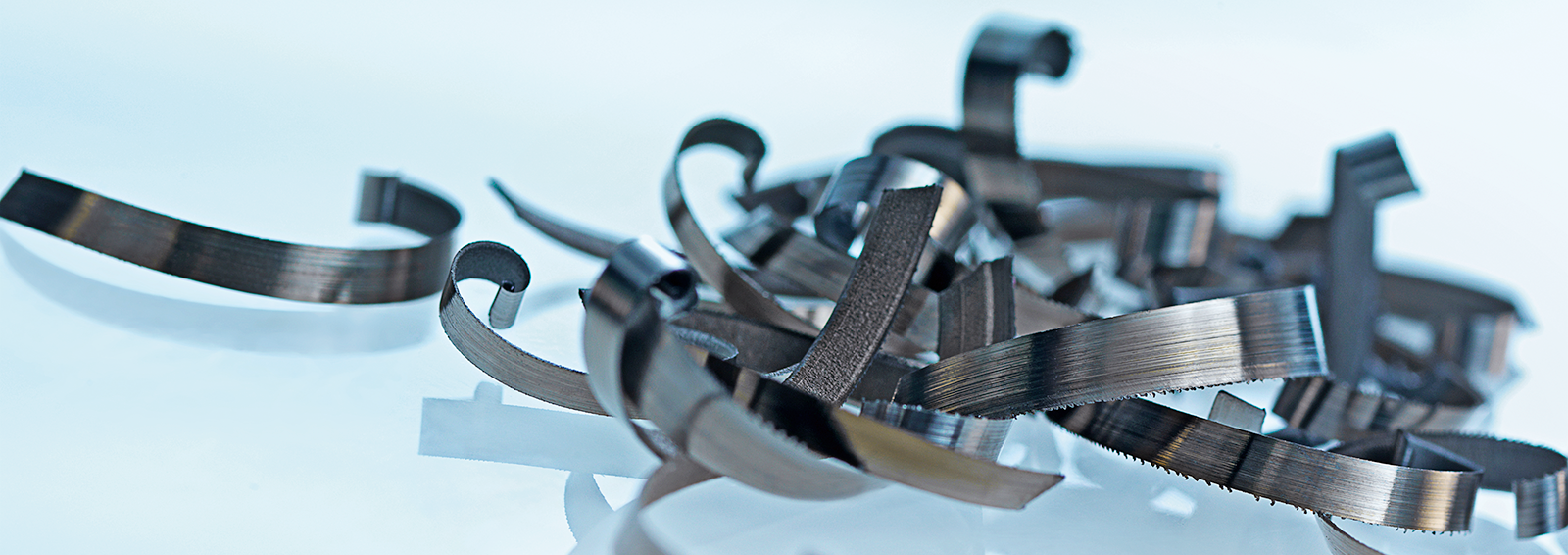
25 ans de Multidec – Le profit durable de votre entreprise se trouve sur le fil du tranchant
Une interview de Mario Macario, Directeur Commercial, et Roberto Nicoli, Chef de Segment, au sujet de multidec® la marque d’UTILIS AG
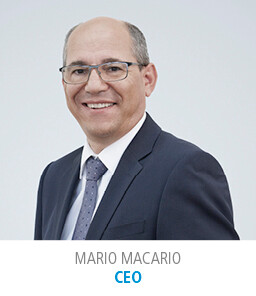
Monsieur Macario, vous avez été engagé chez UTILIS au début des années 90, en pleine période de crise économique; vous étiez alors un jeune directeur commercial, et avez commencé votre activité dans une situation assez délicate. Dans ce contexte vous avez redressé la barre d’UTILIS en lançant le projet multidec®.
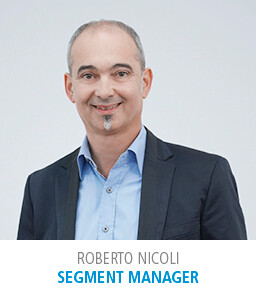
Monsieur Nicoli, vous avez rejoint UTILIS en 1997 en tant que jeune chef de produit, et l’on peut dire, que vous êtes aujourd’hui l’encyclopédie vivante de multidec® chez UTILIS. Jusqu’aujourd’hui vous avez construit toute la gamme connue de multidec®, vous l’avez constamment améliorée et développée.
Ces 25 ans de multidec® comptent beaucoup, il s’agit d’une longue période, qui vous a tous deux très certainement marqués. Nous voudrions en savoir un peu plus sur cette période passée, ainsi que sur les projets futurs.
Quel a été l’élan, l’élément déclencheur du lancement et du développement d’une propre gamme d’outils d’usinage pour les pièces de petites dimensions ?
Macario La grave crise économique du début des années 90, durant laquelle le chiffre d’affaires avait chuté de plus de 30%, nous a amenés à revoir notre stratégie. La société UTILIS s’était principalement concentrée sur le commerce d’outils de précision en Suisse durant les années 70–80. La production de produits finis en interne avait été mise de côté, et n’atteignait qu’une part minime du chiffre d’affaires en Suisse. L’étude de marché démontra qu’il ne fallait pas rester si dépendant de la distribution et qu’il ne fallait pas se contenter uniquement du marché Suisse, pour pouvoir se projeter à long terme.
L’industrie horlogère connu alors une nouvelle impulsion avec le lancement de SWATCH, les producteurs de microcomposants mécaniques pour les montres ont alors connu un nouveau souffle. Dans le même temps, les composants pour la technique médicale se sont développés, avec l’arrivée des implants dentaires, des prothèses et broches pour la chirurgie osseuse. La demande de tels produits a augmenté de façon conséquente ; des pièces en titane et en inox, des matières difficiles à usiner, étaient travaillées alors à l’aide de burins brasés, lesquels devaient être affûtés et brasés par les utilisateurs, un véritable défi. Mais le procédé de réaffûtage et de brasage était déjà sur le déclin, avec l’arrivée des plaquettes de coupe amovibles, lesquelles permettaient alors un changement rapide de l’outil ; C’est ainsi que les plaquettes amovibles ont remplacé les outils brasés.
Avec le développement de la technologie à commande numérique CNC sur les tours à poupée mobile, le développement de nouveaux outils coupants était devenu nécessaire ; ces outils demandaient de grandes exigences de précision.
Ces enjeux et facteurs recueillis débouchèrent sur la décision de se lancer dans le développement et la production d’outils coupants destinés à l’industrie du décolletage, pour les machines mono- et multibroches, une solution idéale pour se lancer sur un marché à dimension internationale. Nous nous sommes lancés dans sur ce marché avec le slogan suivant: «Le profit durable de votre entreprise se trouve sur le fil du tranchant».
Nicoli Avec la fin des machines à cames et la transition vers les machines à commande numérique CNC, et avec des exigences de plus en plus accrues pour des pièces de petites dimensions, nous nous sommes lancés dans le développement d’une gamme d’outils adaptés à des exigences très élevées. En outre, l’arrivée de la technologie CNC a rendu possible la production de pièces de petites dimensions en petites séries plus flexible et plus rapide. Afin de pouvoir contribuer à l’optimisation de la productivité, et à la baisse des coûts de production, les opérateurs sur machines ne voulaient alors plus passer de temps à réaffûter eux-mêmes leurs outils coupants, mais plutôt utiliser des outils précis et rapides à changer et à régler. À partir de ces enjeux, la gamme multidec® a été développée rapidement.
Quelle stratégie a été alors adoptée ? Vient-elle de l’externe vers l’interne ou l’inverse ?
(Les idées viennent-elles du marché, ou essaie-t-on de développer un nouveau marché à partir d’idées nouvelles ?)
Macario Clairement de l’externe vers l’interne. Nous dialoguons avec nos clients et les écoutons avec attention. Leurs problématiques, leurs enjeux et souhaits sont notés avec attention dans notre cahier des charges. Nous essayons alors de tester les technologies les plus récentes dans le monde des outils de précision, afin de les adapter au mieux aux exigences de la mécatronique et de l’usinage des petites dimensions.
Nicoli À partir des informations collectées sur le terrain, nous formons des groupes de travaux, et nous nous retrouvons régulièrement pour discuter et décider des exigences et des priorités que nous devons établir. Les projets engagés sont menés à maturité, puis appliqués de façon à concevoir les outils les plus efficaces possibles pour les clients.
Lorsque vous regarder dans le rétroviseur, quels ont été pour vous les jalons/les plus grands succès durant ces 25 années ?
Macario Nous avons lancé multidec®-CUT en 1993, avec une ligne de plaquettes de formes classiques pour des applications de tournage extérieur sur des machines à poupée mobile. Ensuite la ligne multidec®-TOP a été lancée ; il s’agit de plaquettes ISO à face plate large sur l’arête de coupe, conçues pour dresser et charioter.
Puis vint s’ajouter la ligne ISO, pour répondre à une demande toujours plus importante, avec des plaquettes aux géométries de brise-copeaux optimales, aux rayons inférieurs à 0.2 mm, et des nuances de carbure adaptées à l’usinage de pièces de petites dimensions. Dans le même élan, des porte-outils fins, adaptés aux nécessités techniques, ont été développés et ajoutés à la gamme de produits standard de multidec®-ISO.
Au même moment, la question de l’usinage intérieur de trous de diamètres 0.5 à 8 mm fût soulevée, et ainsi la ligne multidec®-BORE MICRO vint s’ajouter à une gamme standard alors déjà très élargie.
Durant la crise financière de 2008, certains de nos clients ont cherché, notamment dans le domaine de la technique médicale, à atteindre des coûts de production plus économiques pour la réalisation de vis chirurgicales par opération de tourbillonnage avec plaquettes amovibles. Il s’agit d’un processus de fraisage, et il était clair pour nous, qu’un système d’outil munit de plusieurs plaquettes de coupe devait être développé dans ce domaine, afin de réduire les coûts de production. Avec multidec®-WHIRLING nous pouvions alors répondre aux demandes des clients, en proposant un anneau de tourbillonnage munit de 12 plaquettes de coupe dans un cercle inscrit de 12 mm, avec une baisse des coûts de production atteignant 80%. Le prix des plaquettes devint alors secondaire. Dans ce contexte, nous avons révolutionné le marché à l’international, et les nombreuses tentatives d’imitation de nos concurrents n’ont fait que confirmer notre succès.
Nicoli Comme nous l’avons déjà dit, le lancement de multidec®-CUT est et a été un succès, tout comme l’arrivée de multidec®-TOP. Le nom «TOP» est pertinent, car ces plaquettes sont encore un produit phare après 25 ans.
Mais une autre étape clé fut aussi le lancement de la ligne multidec®-CUT 3000 en 2003. Ce nouveau système reprenait l’ensemble des développements techniques opérés ainsi que l’expérience du terrain acquise jusqu’à présent, tout en corrigeant les faiblesses des systèmes existants. La nouvelle ligne multidec®-CUT 3000 était aboutie, et s’est imposée sur le marché à une grande vitesse, nous permettant de remplacer très rapidement les anciens systèmes.
Ces dernières années nous nous sommes concentrés sur le processus d’usinage coupant. Ici nous rencontrons des défis avec la température engagée par la plaquette de coupe sur la matière, qui compromet la durée de vie de l’outil, ainsi que le contrôle du dégagement du copeau. Nous suivons de près les problématiques de la profession, et n’hésitons pas à utiliser ici les dernières technologies développées en termes de performances de lubrification haute-pression, et développons des systèmes d’outillages à arrosage intégré pour les machines à poupée mobile. L’enjeu de concevoir des conduites de lubrification internes et des points de connexion à la pompe sur des outils à structures très fines et étroites, tout en permettant une orientation exacte de l’arrosage sur l’arête de coupe, pouvait nous amener à développer un système très onéreux. Le système breveté de cale multidec®-LUB, avec canal de lubrification intégré, apparait comme un investissement pertinent pour le positionnement des outils dans la machine. Le client peut continuer à utiliser ses outils conventionnels. La valeur ajoutée réside dans les butées à arrosage intégrées, permettant un positionnement précis de l’outil sur la cale, ainsi qu’un changement rapide.
Y a-t-il eu des échecs ?
Nicoli Le processus de développement d’un produit doit toujours être suivi de près, afin de savoir si nous prenons la bonne direction, ou si nous devons procéder d’une manière différente. Néanmoins, par chance nous n’avons jamais connu d’échec critique. L’expérience et les connaissances que nous avons accumulées au cours de toutes ces années dans notre domaine d’activité, nous ont permis d’éviter de commettre des erreurs coûteuses.
Macario Naturellement nous ne pouvons pas appliquer comme souhaité l’ensemble de nos idées. Parfois certains projets doivent être arrêtés au stade de développement, et nous devons parfois arrêter une ligne de produits, car les besoin du marché ont été mal évalués. En tant qu’entreprise nous devons malgré tout prendre des risques, afin de pouvoir être durablement compétitifs.
Quelles sont les perspectives ?
Nicoli L’environnement économique et technologique changent très rapidement; l’industrie 4.0, avec les nouvelles technologies d’impression laser, la fabrication additive, le prototypage rapide etc., vont vraisemblablement nous amener à relever de nouveaux défis. Avec les changements dans le domaine des transports et de la mobilité, la fin du moteur à explosion et le futur avènement du moteur électrique va se traduire par une baisse de la demande en composants mécaniques pour l’automobile, à long terme. Ainsi cela aura un impact sur l’industrie d’usinage coupant et par conséquent sur les besoins en outils. Il y aura de nouvelles opérations, que nous devrons appréhender et envisager. Il s’agira dans tous les cas d’une nouvelle ère passionnante et intéressante pour notre nouvelle génération de techniciens compétents, qui devra être à la hauteur de ces nouveaux enjeux techniques et stratégiques.
Macario L’industrie 4.0 ouvre aussi de nouvelles perspectives pour nos connaissances techniques, à travers une nouvelle forme de communication nous permettant d’être à la disposition des utilisateurs de manière toujours plus efficace. Ainsi nous pourrons à l’avenir proposer à nos clients des éléments utiles, des informations et des solutions qui pourront être collectées à partir de notre E-Shop.
Avec la livraison prochaine d’un nouveau bâtiment, vous allez doubler votre capacité de production. Où songez-vous trouver de nouveaux marchés pour la gamme multidec® ?
Macario La taille du marché à l’échelle mondiale va pour le moment rester la même. L’industrie 4.0, qui se base en grande partie sur l’automatisation et l’utilisation de robots, va très sérieusement influencer le domaine de la micromécanique. Les éléments pour petits moteurs électriques, et pour éléments de transmission etc., seront toujours très demandés, et ces pièces seront toujours usinées sur des tours automatiques. Or, outre l’Europe et l’Asie, je vois particulièrement un potentiel de croissance en Chine et aux États-Unis.
Nicoli Avec des pièces de plus en plus complexes, des matières modernes difficiles à usiner et des dimensions toujours plus petites, il y’aura toujours une demande très spécifique pour les outils de haute précision. Il y’a dans le domaine de la micromécanique un potentiel de croissance qui demeure conséquent dans le futur. Beaucoup de microcomposants sont utilisés dans les domaines de l’électronique et de l’informatique. Aussi, le potentiel de développement de la technique médicale va continuer à croître. Ici les nouveaux matériaux représenteront à l’avenir un enjeu important. En proposant des solutions intelligentes dans toutes ces branches, nous aurons de bonnes chances de répondre présents. Afin de pouvoir relever ces défis majeurs, nous avons besoin d’un parc machines moderne, avec une capacité de production suffisante. Avec ces nouveaux projets, nous nous préparons d’ores et déjà à l’avenir.
Dans ce segment de marché, quelle est la force et la taille de la concurrence ?
Macario Elle est très dense, comme dans toutes les branches. Cependant, cette concurrence est intéressante et stimulante. Dans l’usinage coupant de petites pièces, les tolérances sont très minces et la réduction de la pression de coupe déterminante. C’est pourquoi les sociétés suisses, allemandes et japonaises se sont imposées en premières, car elles se sont exclusivement concentrées sur ces points.
Nicoli La concurrence n’est, eu égard au nombre des sociétés, pas si grande. Nous sommes ici sur un marché de niche, le marché intéresse moins les gros fournisseurs d’outils carbure. La plupart de nos concurrents, qui sont des sociétés de taille similaire à la notre sur ce marché, développent et proposent également de très bons produits. Nous observons et suivons de près leurs activités et leurs tentatives, et nous nous efforçons de trouver des solutions plus rentables et profitables pour les clients, afin de toujours conserver une longueur d’avance.
l’ÉQUIPE DE DÉVELOPPEMENT
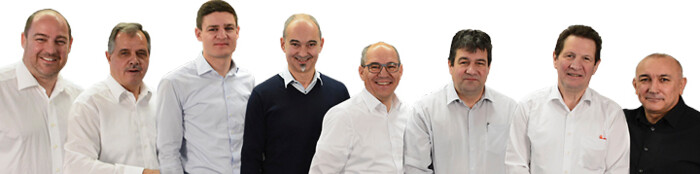
De gauche à droite : Matthias FILIPP, Alexander STÄMPFLI, Thomas FORRER, Roberto NICOLI, Mario MACARIO, Yves JUILLERAT, Denis JUILLERAT et Carmine FABOZZI.